Nachhaltigkeit und Motorsport scheinen auf den ersten Blick nicht immer zusammenzupassen – doch das Forze Hydrogen Racing Team zeigt, dass es anders geht. Das studentische Team mit 45 engagierten Freiwilligen arbeitet an der Entwicklung des Forze 9, eines wasserstoffbetriebenen Le-Mans-Prototyps. Das Ziel: saubere Antriebstechnologien im Rennsport vorantreiben und neue Maßstäbe für nachhaltige Hochleistungsfahrzeuge setzen.
Um ihre ambitionierten Ideen in die Realität umzusetzen, setzt das Team auf 3D Druck – die Technologie um eine schnelle Prototypenerstellung zu schaffen und um iteratives Design und die Fertigung funktionaler Bauteile zu ermöglichen.
3D Druck als entscheidender Faktor in der Fahrzeugentwicklung
Schneller von der Idee zum fertigen Bauteil
Als studentisches Rennteam steht Forze vor den gleichen Herausforderungen wie große Automobilhersteller – jedoch mit begrenztem Budget und ohne industrielle Fertigungskapazitäten. Herkömmliche Methoden wie CNC-Fräsen wären zu teuer und zeitaufwendig. Der 3D-Druck ermöglicht es dem Team, direkt im eigenen Haus zu produzieren und so Entwicklungszyklen erheblich zu verkürzen.
Ein zentrales Werkzeug im Forze-Werkstattbetrieb ist der Method XL 3D-Drucker. Dank seiner großen Bauplattform (305 x 305 x 320 mm) und dem Dual-Extruder-System kann das Team große und komplexe Bauteile effizient drucken. So lassen sich Passgenauigkeit und Funktionalität schnell testen, bevor die Teile endgültig in den Rennwagen integriert werden.
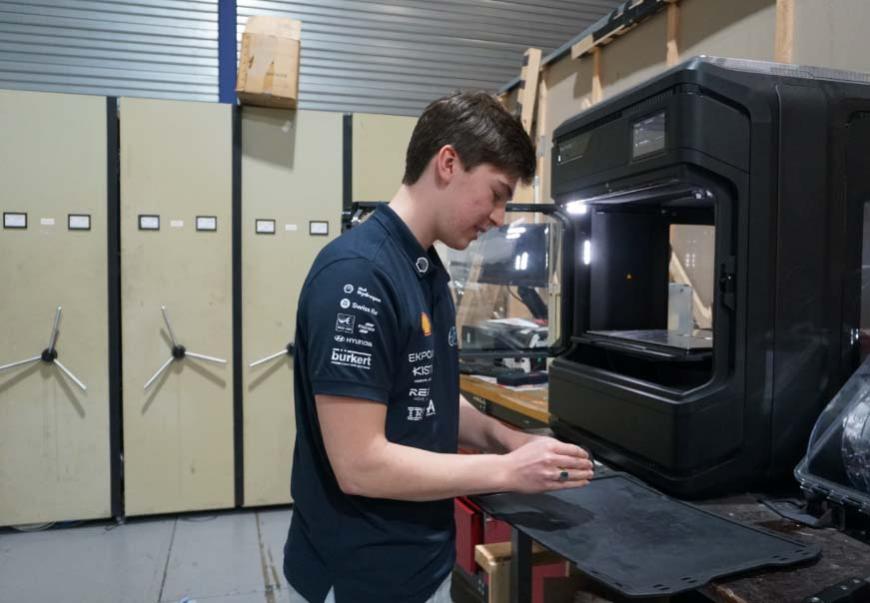
Leicht, stabil und widerstandsfähig – Materialvielfalt im Einsatz
Je nach Anwendung kommen verschiedene Materialien zum Einsatz:
- ABS wird für Prototypen genutzt, da es robust und einfach zu verarbeiten ist.
- Kohlefaserverstärkte Materialien werden für strukturrelevante Bauteile verwendet, die hohe Festigkeit bei geringem Gewicht erfordern.
- Rapid Rinse Stützmaterial ermöglicht den Druck komplexer Geometrien, da es sich rückstandslos in warmem Wasser auflöst.
Durch den gezielten Materialeinsatz können hochbelastbare und gleichzeitig leichte Komponenten gefertigt werden – ein entscheidender Vorteil im Rennsport.
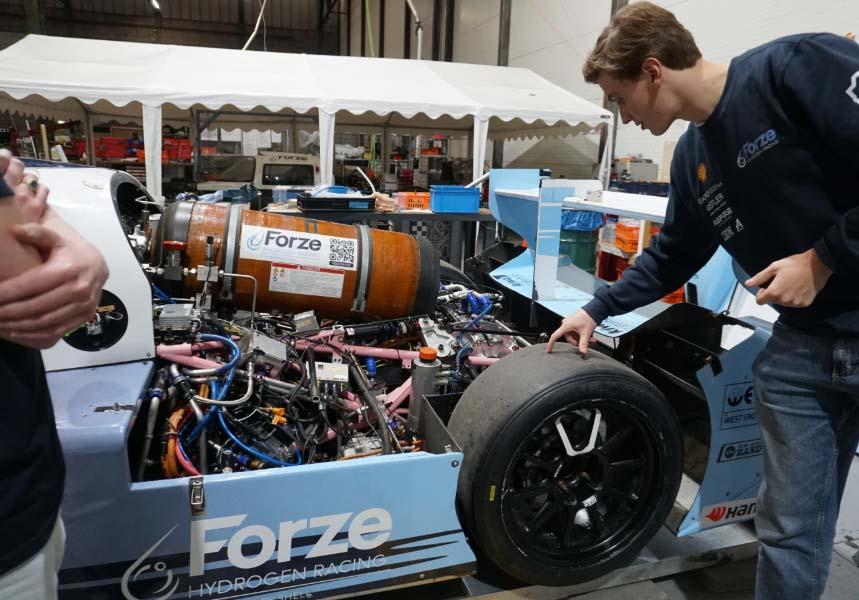
Veränderte Zusammenarbeit im Team
Was als einfache Möglichkeit zur Prototypenerstellung begann, hat sich schnell zu einem integralen Bestandteil der Fahrzeugentwicklung entwickelt. 3D-Druck wird inzwischen in verschiedenen Bereichen des Teams genutzt – vom Chassis-Design über die Fertigung bis hin zur Validierung neuer Konzepte.
Auch der Wissensaustausch hat sich verändert:
Interner Support-Kanal: Erfahrene Mitglieder helfen Neulingen bei Slicing-Einstellungen und Materialfragen.
Digitale Fertigungsplattform: Ein Teammitglied verwaltet die 3D-Druck-Workflows und unterstützt bei der Fehlerbehebung.
Hands-on-Erfahrung: Studierende erwerben wertvolle Kompetenzen im Bereich additiver Fertigung, die ihnen im späteren Berufsleben zugutekommen.
„Wir haben viel gelernt“, sagt Ernst Paardekooper, einer der Forze-Ingenieure. „Auch wenn der Drucker intuitiv ist, gibt es Feinheiten – insbesondere bei den Materialeinstellungen. Durch den Austausch im Team können wir Probleme schnell lösen.“
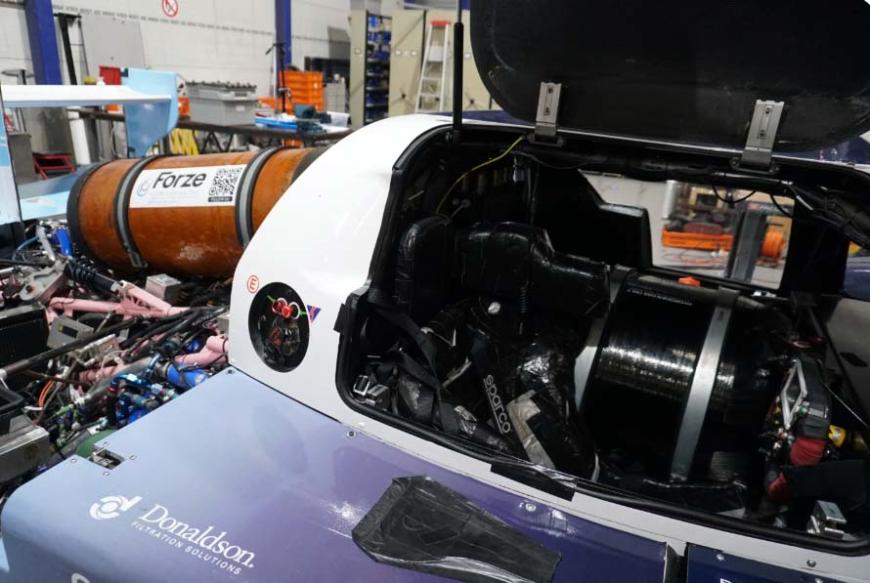
Noch mehr 3D gedruckte Bauteile im Einsatz
Mit den positiven Erfahrungen wächst auch die Nutzung von 3D-Druck. Das Team plant, noch mehr Strukturbauteile und Sonderanfertigungen zu drucken. Koen Vogels, Chief Chassis, bestätigt: „Wir drucken jetzt schon viel mehr als zu Beginn. In Zukunft wird der 3D-Druck eine noch größere Rolle spielen, besonders bei strukturellen Komponenten.“
Wettbewerbsvorteil durch 3D-Druck:
✔ Schnellere Entwicklung und Iteration von Bauteilen
✔ Höhere Designfreiheit für aerodynamische und mechanische Optimierungen
✔ Kostenersparnis durch Inhouse-Produktion
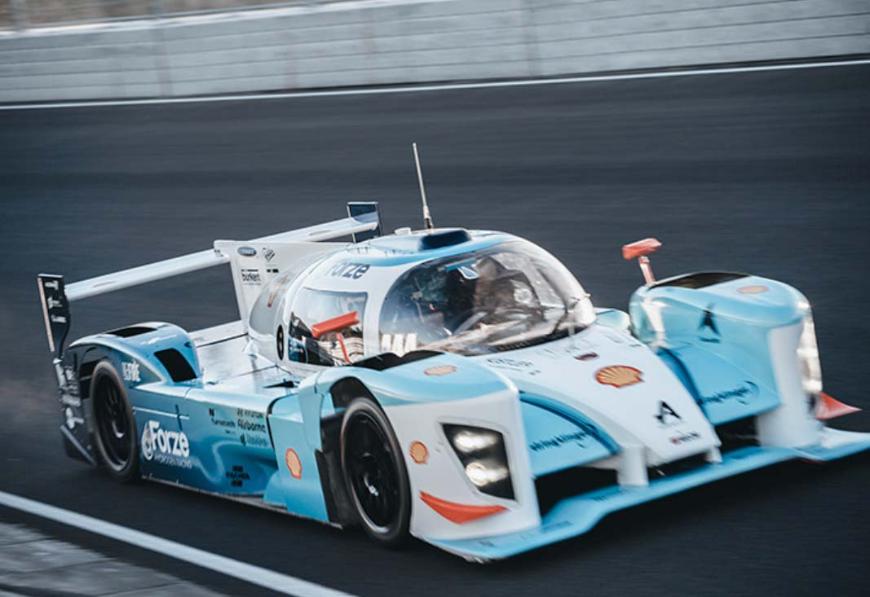