Innovation trifft Tradition
Die Snowboard-Industrie ist geprägt von großen Marken und starken Konkurrenten. Das Rome Snowboard Design Syndicate zeigt jedoch, wie ein unersättlicher Innovationsdrang und modernste Technologien wie der 3D-Druck auch einem kleineren Unternehmen den entscheidenden Vorsprung verschaffen können. Durch die Einführung eines
Formlabs Fuse1 hat Rome Snowboards seinen Produktentwicklungsprozess optimiert - und beweist, dass Kreativität und Effizienz den Unterschied machen.
Zeit und Wettbewerb
Rome Snowboards ist bekannt für seine maßgeschneiderten Bindungen und individuellen Designs. Doch wie bei vielen kleinen Unternehmen stellte die herkömmliche Prototypenfertigung eine große Hürde dar. Vor der Einführung des 3D-Drucks wurde auf manuell gefertigte Tonmodelle oder externe Fertigungsdienstleister zurückgegriffen. Dies hatte gleich mehrere Nachteile:
- Lange Wartezeiten durch externe Anbieter
- Verzögerte Test- und Validierungsprozesse
- Eingeschränkte Kontrolle über Design-Iterationen
„Unsere Entwicklungszeit hing davon ab, wie schnell wir die Teile zurückerhielten,“ erklärt Justin Frappier, Produktdesigner bei Rome Snowboards. In einer Branche, die stark von Innovation und schnellen Anpassungen lebt, war dies ein klarer Wettbewerbsnachteil.
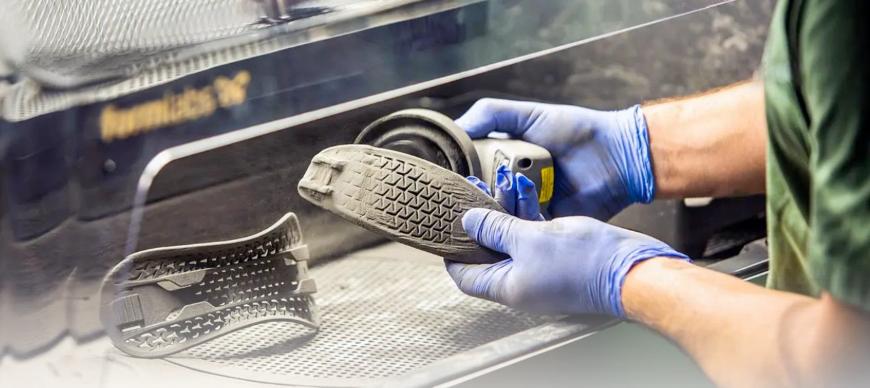
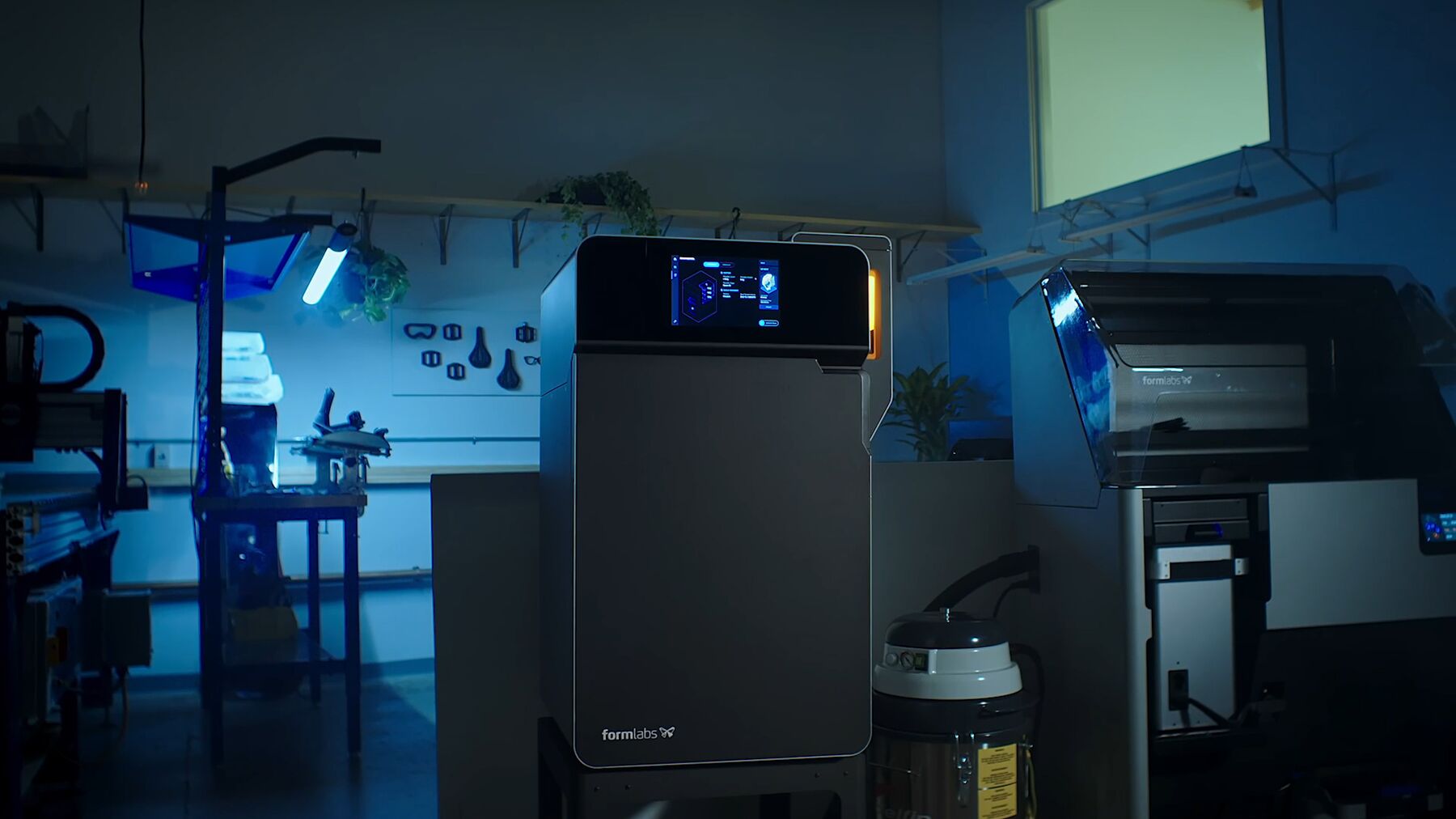
Der Fuse1 3D-Drucker
Nach einer umfassenden Evaluation entschied sich das Team für den Formlabs Fuse1, einen kompakten und kosteneffizienten SLS-3D Drucker. Für Rome Snowboards war der Fuse1 die ideale Lösung:
- Präzise Prototypen: Passform- und Funktionstests sind direkt im Unternehmen möglich.
- Robuste Druckteile: Die Prototypen halten realen Testfahrten auf der Piste stand.
- Schnelle Iterationen: Designs können innerhalb weniger Stunden angepasst und erneut getestet werden.
„Heute drucken wir, fahren eine Runde und drucken am nächsten Tag etwas Neues,“ berichtet Frappier begeistert.
Prototypen auf der Piste
Ein besonderer Vorteil von Fuse1 ist die Robustheit der gedruckten Teile. Die Prototypen können nicht nur auf dem Reißbrett, sondern auch in der Praxis getestet werden:
- Testabfahrten garantieren, dass jede Bindung den extremen Belastungen am Berg standhält.
- Iterationen erfolgen in Echtzeit, ohne Verzögerungen durch externe Dienstleister.
- Konstruktionsfehler werden frühzeitig erkannt und kostspielige Anpassungen vermieden.
Durch die schnelle Validierung gewinnt Rome Snowboards wertvolle Wochen im Entwicklungsprozess - ein entscheidender Vorteil gegenüber der Konkurrenz.
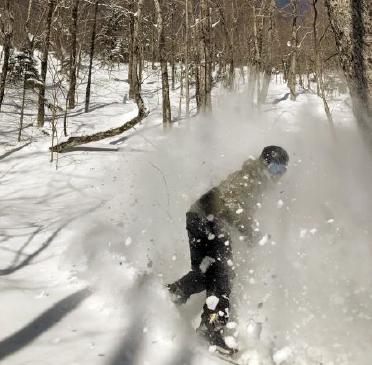
Mehr Tempo, mehr Innovation
Seit der Integration der Fuse1 hat Rome Snowboards Entwicklungskapazitäten erheblich gesteigert. Die wichtigsten Ergebnisse auf einen Blick:
- Beschleunigte Produktentwicklung: Der komplette Entwicklungszyklus wird im eigenen Haus abgewickelt.
- Verbesserte Qualität: Praxisnahe Tests garantieren die Festigkeit und Flexibilität der Bindungen.
- Wettbewerbsvorteil: Rome Snowboards kann schneller auf Trends reagieren und innovative Designs auf den Markt bringen.
3D-Druck als Schlüssel zum Erfolg
Rome Snowboards beweist, wie additive Fertigung kleinen Unternehmen dabei helfen kann, mit den Branchenriesen zu konkurrieren. Durch den Einsatz der Formlabs Fuse1 konnte das Designteam nicht nur Entwicklungszeiten drastisch verkürzen, sondern auch die Qualität seiner Produkte auf ein neues Niveau heben.
Mit einem innovativen Ansatz, einem klaren Fokus auf Effizienz und der Leidenschaft für das Snowboarden zeigt Rome Snowboards, wie der 3D-Druck zum echten Gamechanger wird –
auf der Piste und im Wettbewerb.